Although capacitive fill sensing is quite standard in industry, SEB is one of the only few collegiate teams in the world to have mastered that technology. Our capacitive fill system precisely detects the fill levels in our propellant tanks using sensors that stick down into the tanks and measure the capacitance change as tanks are filled with liquid. This system allows us to use and fill our tanks with non-cryogenic liquids such as propane. Our previous system of measuring tank fill, which sensed temperature change, could only be used for cryogenic liquids. Our flow rate data is also much more accurate, which is great for our simulations and engine development calculations.
“It’s really amazing to think that our sensors, made of just a few pieces of steel and plastic, will be able to tell us precisely how full our tanks are. Capacitive fill has been something that's been talked about in the club for quite a long time, so even as a new member, seeing it come to fruition feels pretty special.” - Justin Yang, SEB avionics engineer (2021-2022) behind the capacitive fill sensor
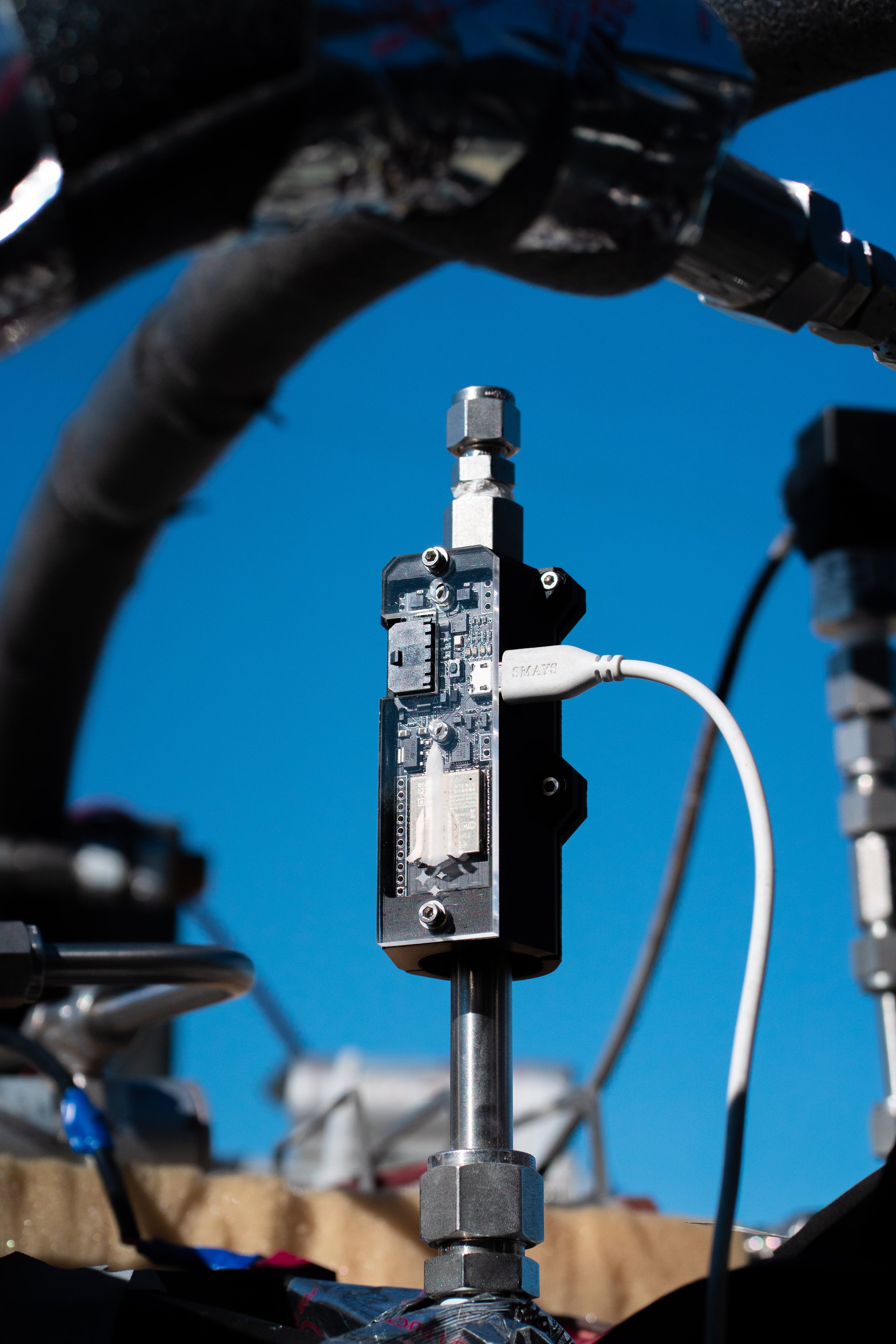
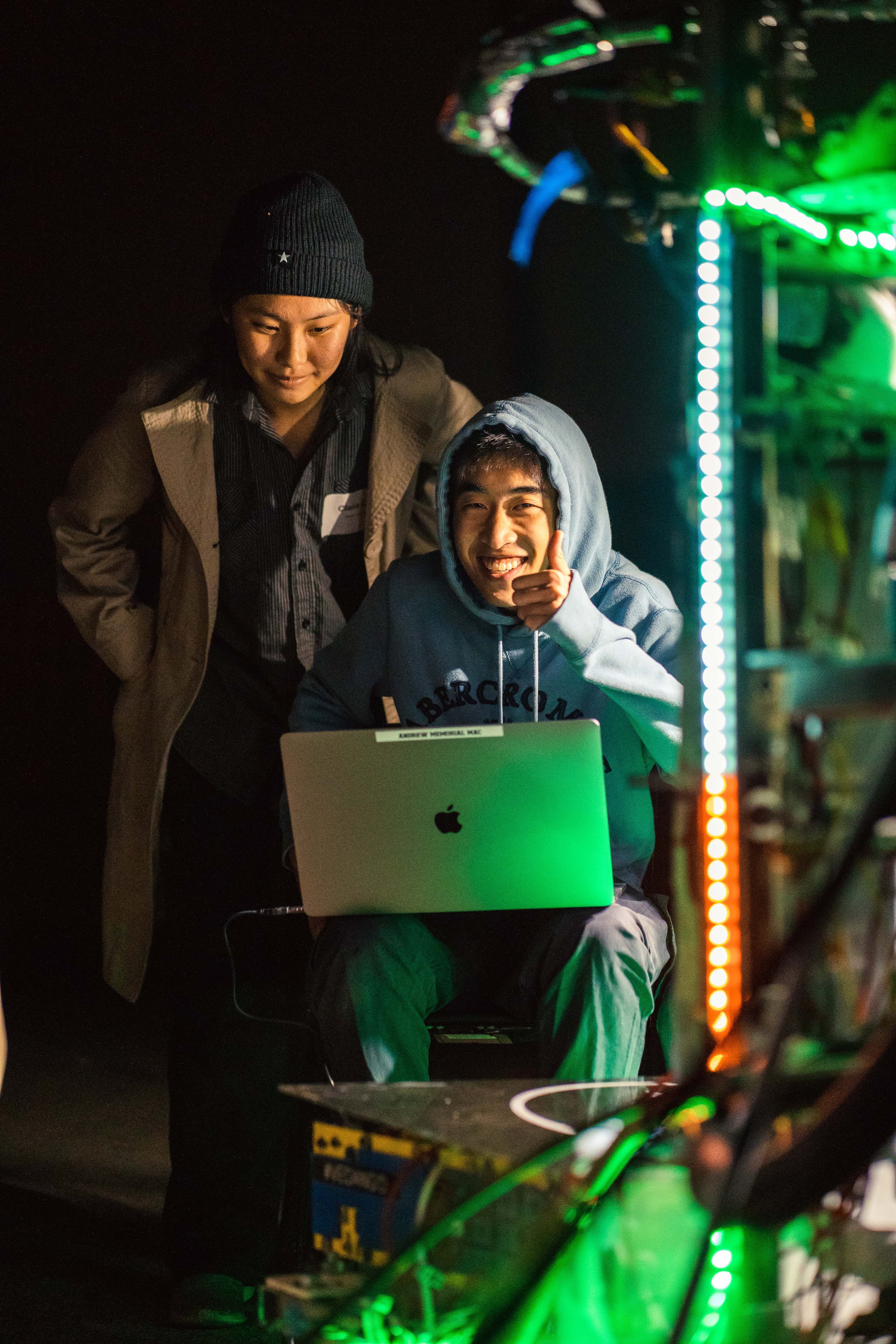
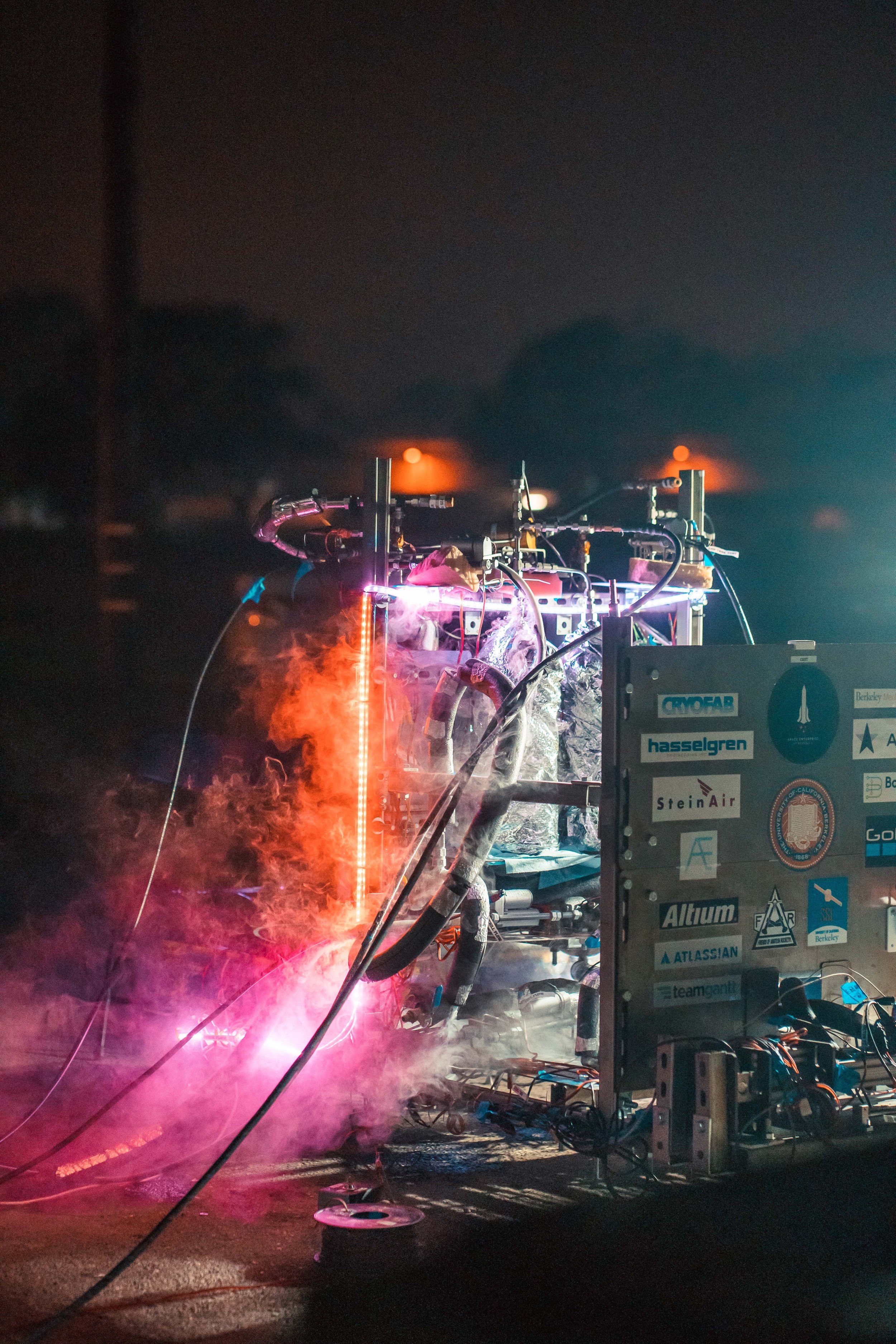
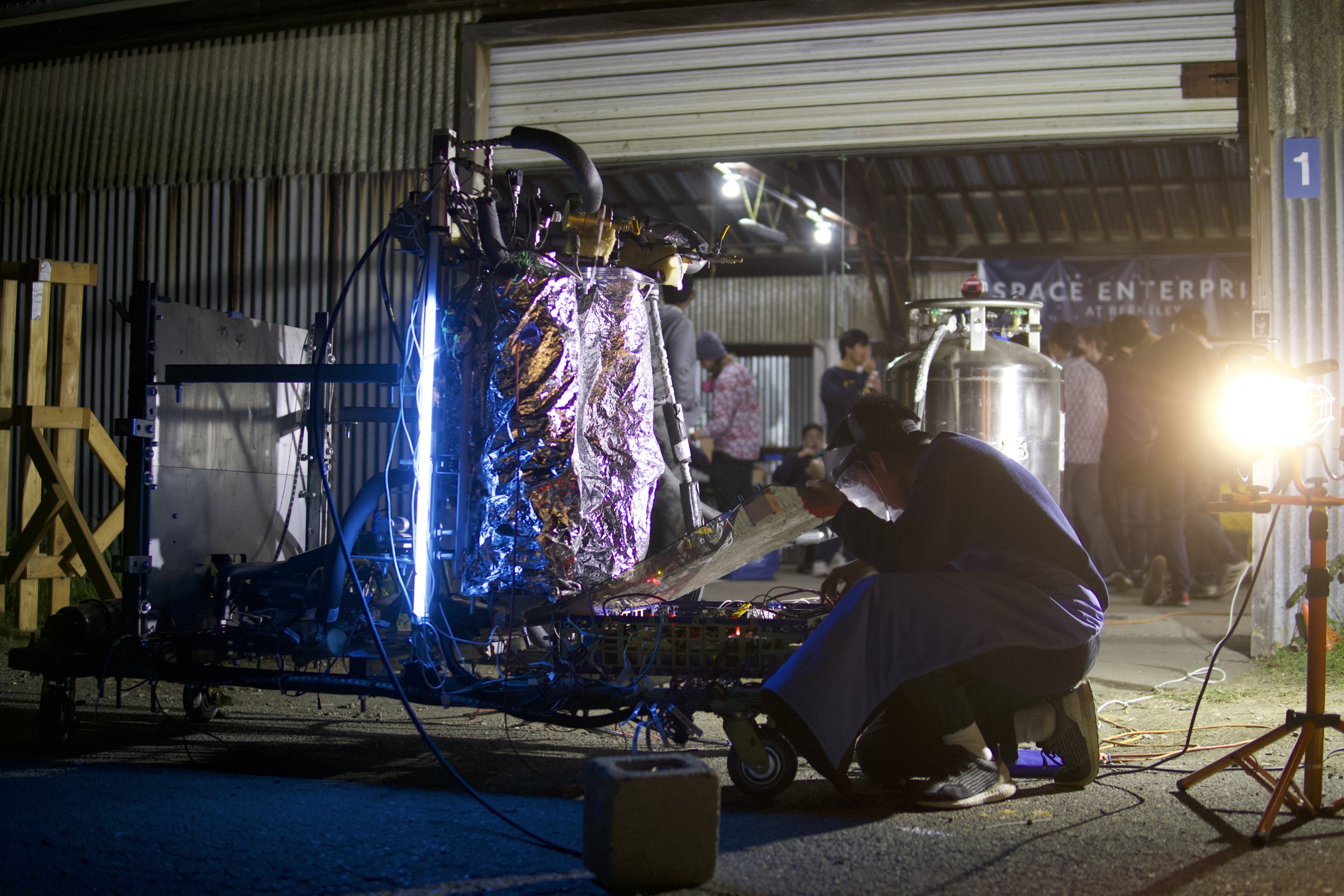
Technical HIGHLIGHT
How was “Cap Fill” made?
We make use of a custom capacitor made up of two concentric cylinders, evenly spaced throughout via teflon spacers. One such capacitor is placed within each of our propellant tanks, extending from the top to nearly the base of the tank. As propellant is filled, the capacitance of each capacitor changes due to the change in relative permittivity of the dielectric in between the cylinders. The relative permittivity of the dielectric is given by a weighted average of the two materials in between the cylinders (lox/propane and air). The average is weighted by the proportion of each material between the cylinders - which is a function of fill level. At full, all of the dielectric is propellant. At empty, it is all air. Thus, by sensing the capacitance via a custom PCB, we can sense the fill level of the tanks. Knowing the capacitance of a full tank of propellant versus an empty tank provides sufficient information to characterize the system.
To arrive at this final design, our team of engineers faced significant challenges. Building the capacitor itself was quite complex. Given the capacitor has two plates which need to be electrically isolated in the tank, a cryo-safe and pressure-tight seal must be maintained. Additionally, we also found quantifying the capacitance of the sensor to be quite tedious, as the readings were very low - in the order of tenths of nanofarads. This makes the system very sensitive to noise, such as electromagnetic interference. Even stray pieces of metal (fasteners, brackets...) that get close to the sensor can technically affect readings!